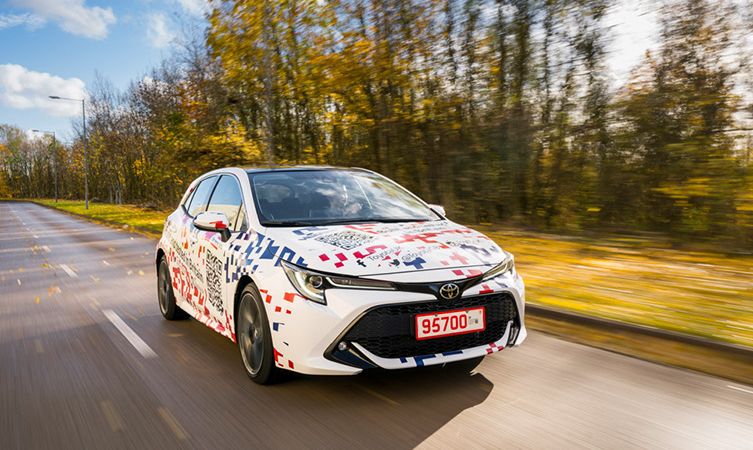
2019 Toyota Corolla: built and tested in Britain
We follow TMUK’s pioneering Quality Assurance department as it pools resources to fine-tune the new 2019 Corolla ahead of production starting at the Burnaston plant.
We follow TMUK’s pioneering Quality Assurance department as it pools resources to fine-tune the new 2019 Corolla ahead of production starting at the Burnaston plant.
Toyota Research Institute will introduce its next-generation automated driving research vehicle at the Consumer Electronics Show.
Toyota intends to achieve a 100% reduction in CO2 in Europe by 2035. Electrified powertrains form the heart of this bold strategy.
We speak to the Toyota People who have worked at our Burnaston factory since it opened 25 years ago.
It started with a spade. Find out how an area of Derbyshire wasteland came to become a powerhouse of sustainable automotive manufacturing way back in 1992.
In years gone by, the ordering bike provided a vital parts delivery tool. See how things have changed.
No, we’re not having a ‘giraffe’; there really is a crossing at TMUK based on the tall and black-tongued creature. Learn about its vital role in Just-In-Time Production here.
Before each steel panel heads off to the weld shop for assembly, a team member will sign their name on the panel, taking both pride and responsibility for their work.
To ensure new car components can be handled quickly and safely, suction cups are used to pick them up.
An on-site crèche keeps member’s children safe and well.
How much solar power do you think Toyota’s Derbyshire factory generates? Find out here.
Casting an engine block requires an enormous amount of thermal energy. Enter TMUK’s part-solar-powered furnace.
Green-fingered folk, discover how Toyota Manufacturing UK has built a nature reserve with a little help from the Royal Botanic Gardens at Kew.
Every Auris and Avensis starts its life as a roll of sheet steel. Here’s how the metal is shaped into a vehicle for the road.