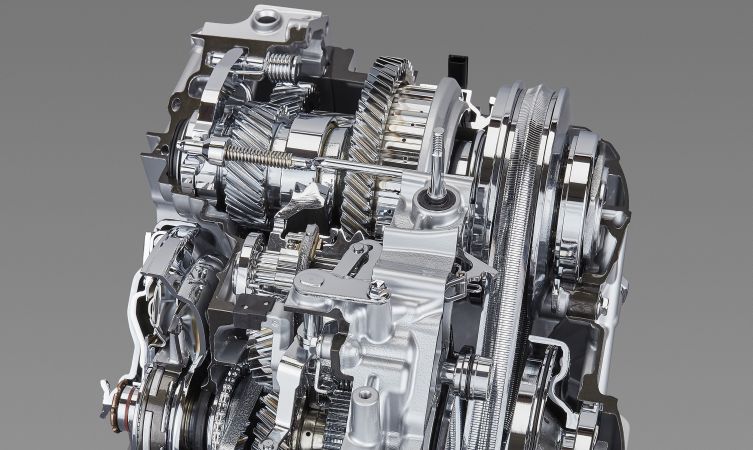
Toyota announces new TNGA-based transmissions, engines and all-wheel drive systems
Toyota has developed a suite of new Toyota New Global Architecture engines, transmissions and all-wheel drive systems.
Want to know all the latest tech news from the world of Toyota? We’ll be bringing you all the details in this section of mag.toyota.co.uk.
Toyota has developed a suite of new Toyota New Global Architecture engines, transmissions and all-wheel drive systems.
Toyota has made the world’s first neodymium-reduced, heat-resistant electric motor magnet. What breakthroughs enabled its development?
Toyota posts sales of 1.52 million electrified vehicles in 2017, three years ahead of schedule.
Toyota launches a new mobility ecosystem and concept vehicle at the 2018 Consumer Electronics Show.
Toyota Research Institute will introduce its next-generation automated driving research vehicle at the Consumer Electronics Show.
Toyota intends to achieve a 100% reduction in CO2 in Europe by 2035. Electrified powertrains form the heart of this bold strategy.
We speak to the Toyota People who have worked at our Burnaston factory since it opened 25 years ago.
It started with a spade. Find out how an area of Derbyshire wasteland came to become a powerhouse of sustainable automotive manufacturing way back in 1992.
In years gone by, the ordering bike provided a vital parts delivery tool. See how things have changed.
No, we’re not having a ‘giraffe’; there really is a crossing at TMUK based on the tall and black-tongued creature. Learn about its vital role in Just-In-Time Production here.
Before each steel panel heads off to the weld shop for assembly, a team member will sign their name on the panel, taking both pride and responsibility for their work.
To ensure new car components can be handled quickly and safely, suction cups are used to pick them up.
An on-site crèche keeps member’s children safe and well.
How much solar power do you think Toyota’s Derbyshire factory generates? Find out here.